Krister Tuhimaa, operator
Krister Tuhimaa from Söderhamn works as an operator in Vallvik and is operator training supervisor for the fourth time. “I went through the same training myself 17 years ago, so I know what they’re going through.”
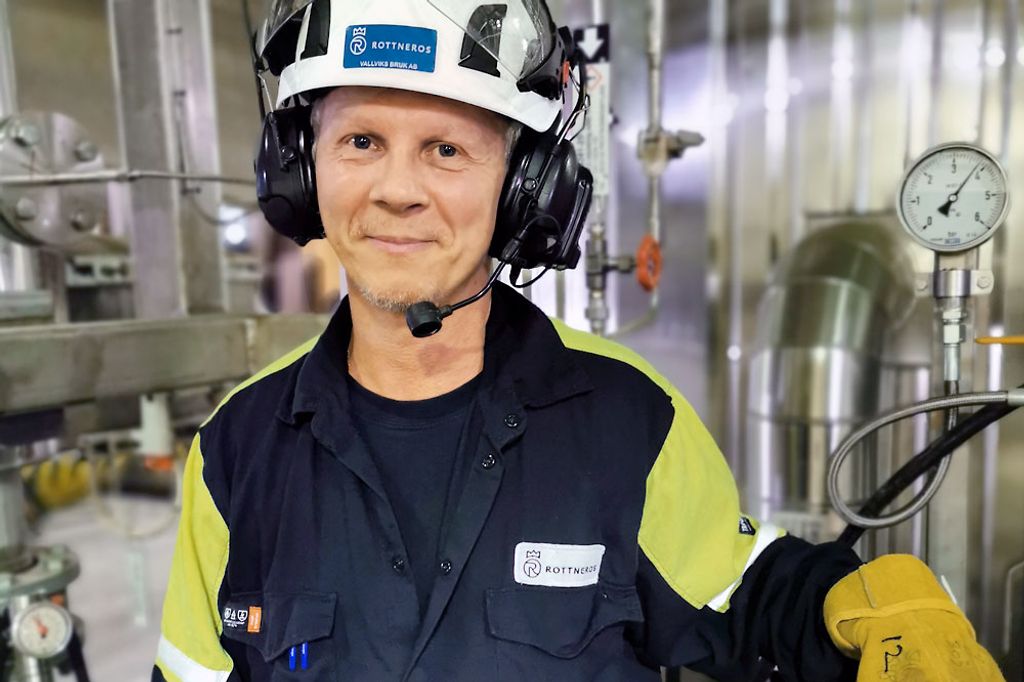
Why are you supervising this training?
“My colleague Örjan and I were requested to supervise as we’ve done this before. Of course, it takes a little more time and commitment from us. You have to explain what you’re doing as you’re doing it. But it’s fun.”
How do you set up the practical training?
“We usually plan things based on how we’d want it to be if we were trainees ourselves. We start at a very basic level and at a slow pace. We gradually increase the level of difficulty while making sure we go over things again and again. It takes both practice and theory. In other words, we go through the manuals that are available. I usually say the worst thing you can do is to say that you understand when you don’t. Ask once too often rather than once too little.”
What’s the hardest part about being a supervisor?
“It can be hard to get an idea of what the trainee understands and doesn’t understand sometimes. You need to be active and ask yourself as a trainee, otherwise we supervisors don’t know how high to set the bar.”
How do you know that trainees have learned everything that they should?
“As it stands now, much responsibility lies with us as supervisors to pass the trainees we’ve taught. We can determine the trainee’s level of competence before they are offered employment. Not everyone is ready to take on responsibility immediately after training. Some trainees may need to be accompanied for a while.
If you leave a new person alone in situations they have no experience of, it can be scary. This is a pretty dangerous workplace with pneumatics, heat and a lot of chemicals. You need to feel comfortable and safe in what you’re doing in order to avoid accidents as much as possible.”
How do you deal with safety?
“Safety has improved a lot over the years, as it’s now a top priority and even put before productivity. Most people are conscientious with all kinds of protective equipment and if anyone has forgotten any protection, we remind them. We take care of each other.”
What’s usually the hardest thing to learn?
“The process as a whole. And it’s often stressful when a lot of things happen at the same time on the monitors and you can’t keep up. Sometimes when you’re sitting all alone, people can come in, call on the radio, and phone you, all at the same time.”
Have you worked with the same colleague the whole time?
“Yes, my colleague Örjan was the one who trained me. I know him better than my own partner and we get along very well. I hope they never split us up!
In fact, the whole shift team gets along very well. Many of us find things to do together in our spare time as well like going to concerts, cycling or sailing etc. We get what’s called ‘shift money’ that goes on activities, which could be used to pay for a cruise for the shift team.”