Magnus Öström, Underhållsingenjör
Magnus has been a maintenance engineer on the recycling line at Vallvik since 2020. His technical background is a great strength in his job, as is his experience from other plants.
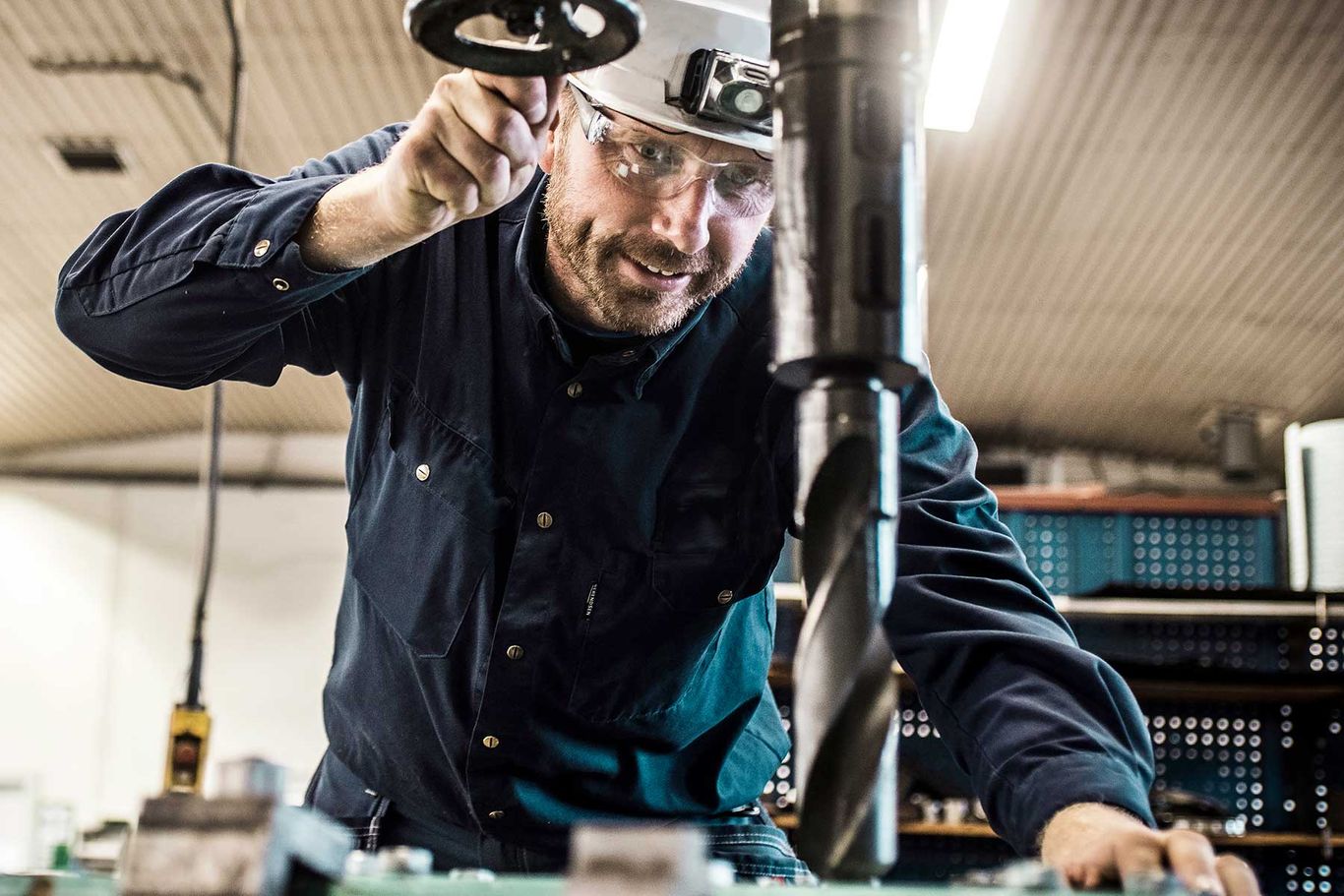
So what does a maintenance engineer actually do at a pulp mill?
- I’m responsible for both remedial and preventative maintenance, which means working at my computer and out at the machines side by side with the operators. Briefly put, I make sure that operations in recycling run as they should, and, ideally, that they become a little better and more efficient every day. A regular day can, for example, involve preparing purchasing and procurement documents, analysis and interpretation of various measurement values or drawings, and much more besides.
Tell us about your department, recycling
- Wow. That’s not easy ... Vallvik Mill is divided into two parts: the fibre line and the recycling line. I work for the maintenance department in recycling. Here, we deal with everything that DOESN’T become pulp, but is recycled and returned to the factory. We also take care of the steam that’s produced during the firing process and channelled through a turbine. A spinning generator converts the motion into electricity, which is then led back to production. My department is also responsible for the cleaning station, where the trunks are debarked and chopped up into woodchip.
What are you doing to reduce electricity consumption even further in your everyday work?
- We generate fully 69 percent of the electricity we use at Vallvik Mill ourselves (2022). And we’re constantly trying to reduce the amount of electricity we purchase. This can, for example, involve replacing an old electric motor with a new, more efficient model, swapping fluorescent lights and filament bulbs with LED lights, or bringing in specialists to maintain and upgrade the turbine. It’s also important to ensure that the operators work to optimise the machines on an ongoing basis.
Can you tell us something about yourself that not everyone knows?
- I applied to be on the reality show “Farmen”, and made it to the second round of interviews. It would have been a quite a challenge but a lot of fun, and I’m sure I would’ve done really well. And my children would have been proud to see their dad on the TV. Another time, I tried to climb Kebnekaise, the highest mountain in Sweden. I made it quite a long way up, but then the weather changed and I never made it to the top. There’s a bit of an adventurer in me, and the next thing I want to try is probably the survival show “Robinson”.
What’s your biggest strength in your current position?
- My technical background is a solid base, especially combined with my experience from several other mills. It allows me to bring in other perspectives, influences and experiences when it comes to the optimisation and development of certain processes and ways of working. This is something that can prove really useful here at Vallvik.
What did you do before starting in your current job?
- I worked at the pulp mill in Norrsundet every summer while I was taking the “Industrial Maintenance” course. Since then, I’ve worked as a welder, mechanic and travelling fitter. I’ve also done several jobs here at Vallvik Mill. When I joined the company in 2012, I was employed as a mechanic on the fibre line, I then moved on to become a planner in recycling and a foreman in the mechanical department. Having such a varied employment history is a real plus, it’s given me a broad overview, combined with hands-on experience from different parts of the business.
What part of your job do you enjoy the most?
- My workmates. It’s fun to work at Vallvik Mill because it's small but big at the same time. It’s quite large and complex, but you soon get to know everyone who works here.
Where do you see yourself five years from now?
- Right where I am today. I just want to keep on going. I want to try to become as familiar as possible with my area – that’s my goal. And to achieve that, I must constantly make sure I’m up-to-date with modern maintenance and process technology by taking different courses at the workplace.