Johan Nabb, operator
Thanks to his drive and support from colleagues, Johan Nabb has progressed to operator at the soda recovery boiler. Here, he shares his journey and what makes Vallviks Bruk a workplace where he thrives and develops.
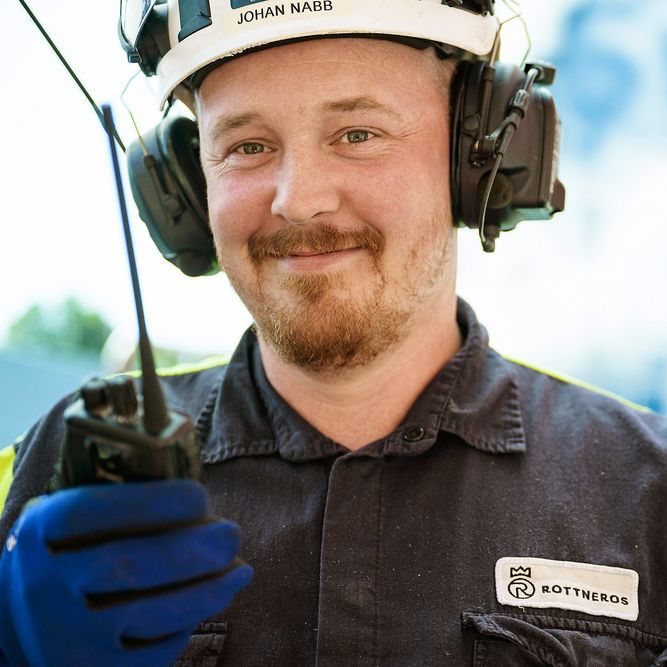
Johan Nabb is currently an operator at the chip plant at Vallviks Bruk. Before that, he worked at Sälls Åkeri, which handles a large part of the transportation within the factory area.
"We did a lot of loading and unloading in the harbor. I had a significant advantage from being a machine operator when I started at the chip plant. Besides monitoring in the control room, we also operate both tractors and forklifts here," Johan explains.
New position and newly awakened interests
But now, a new role with new challenges awaits. Johan is currently training to become an operator at OP4, the soda recovery boiler, a change his boss inspired him to take.
"His enthusiasm was contagious, and now I'm genuinely interested in the entire factory process and how everything is connected. It's complex, but at the same time incredibly exciting," says Johan.
At Vallviks Bruk, the sulfate process is used to produce pulp, a method based on a cycle where raw materials and emissions are purified and reused. The soda recovery boiler, where Johan will work, is an important part of chemical recovery.
The factory is monitored via computer screens in the control center, where operators for OP2-OP5 are gathered and continuously follow the factory's various flows.
"In addition to monitoring, we take turns doing rounds in the factory every other hour to handle tasks that require physical presence."
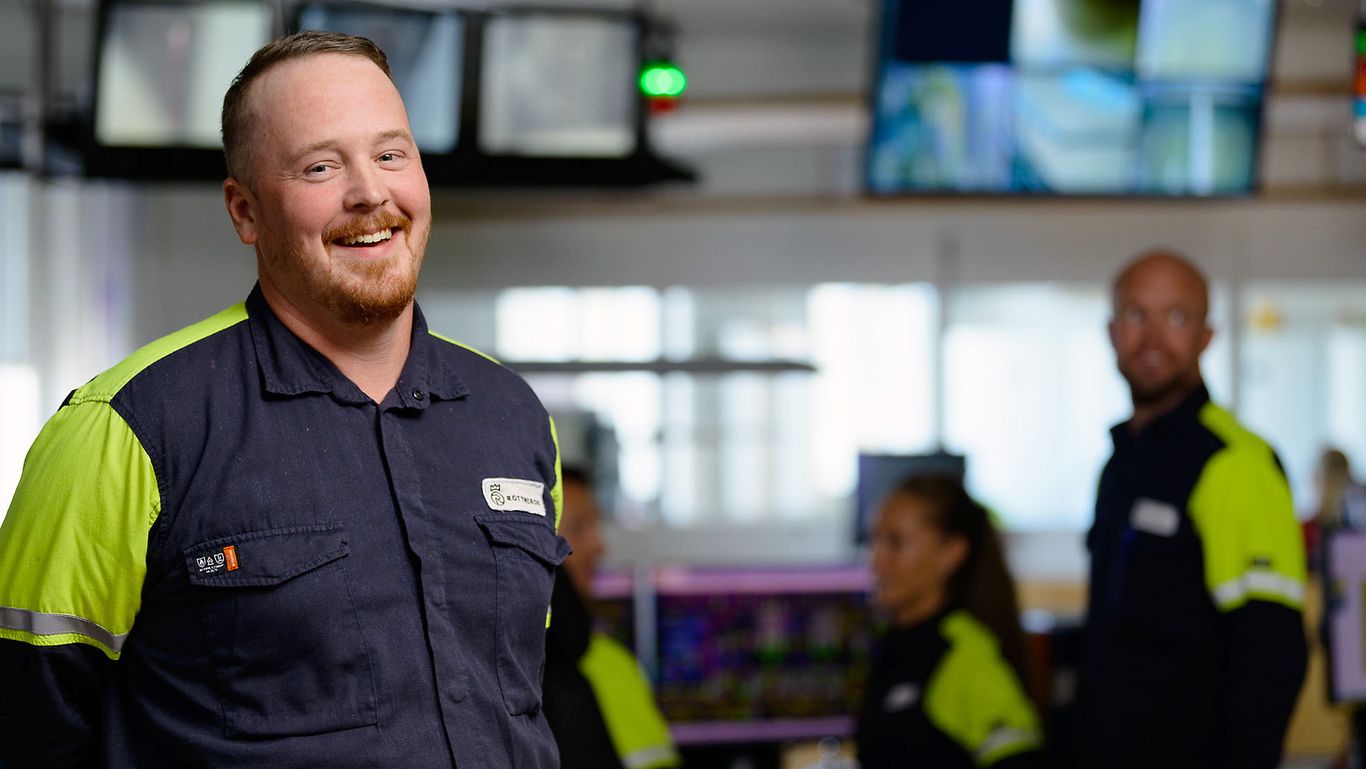
Colleagues who support learning
Johan has spent a lot of time consulting manuals, navigating internal systems, Googling, and walking around the facilities to learn about the different parts of the factory and how they are connected. He has only good things to say about the reception from colleagues when he asks questions and wants to learn:
"The people throughout the factory are incredibly helpful. I think they understand that you don't grasp everything at first. They've been there themselves and know how confusing it is in the beginning. Everyone is willing to help and show you around; I've been treated exceptionally well."
It doesn't matter what you've worked with before - here everything is new
He believes that working in this type of workplace is very unique. If you haven't worked in an identical factory before, everyone has to learn everything from scratch.
"It doesn't really matter what kind of job you've had before. You could have a background as a cashier at ICA, be a hairdresser, or a machine operator—you have to start from square one when you come here," says Johan.
To succeed in the profession, he believes it is important to be attentive and listen to the knowledge that experienced colleagues have. It is also crucial to be able to collaborate, and having an interest in the processes is a plus. Taking care of one’s health is also important when working a six-shift schedule, he says:
“You can’t just sit here at night, pounding a pizza and chugging Red Bull. There’s good health counseling available through the workplace, where you can learn about nutrition, among other things.”
Looking forward to the maintenance shutdown
Johan is also looking forward to being part of this autumn’s maintenance shutdown. It’s an intense week when operations pause, and several hundred suppliers come to the site. Everyone works around the clock to carry out repairs and maintenance measures.
“I think it’s the best and most educational experience you can be part of. All the measures that have been meticulously planned for an entire year must be carried out in as short a time as possible. It’s going to be exciting!”
Great benefits and career development opportunities
What makes Johan enjoy working at Vallviks Bruk so much, beyond great colleagues and interesting tasks? Is there anything else?
“We have good salaries thanks to the shift schedule, but also other benefits like reduced working hours, a profit-sharing foundation, a good wellness allowance, recreational funds, an employee club, and our own gym in Vallvik. Plus, I know that if you want to take courses or further develop within the company, that’s always an option - it’s common here,” says Johan.
“It’s definitely inspiring to see others who have built a career within the company. But right now, I’m happy where I am. I find everything exciting - it’s fun to go to work every day!”